Formula Kentucky
At the beginning of my freshman year, I joined Formula Kentucky, the University of Kentucky’s Formula SAE team. Formula SAE (FSAE) is a collegiate competition hosted by the Society of Automative Engineers (SAE) International. During FSAE competitions, teams are awarded points based on how they present their vehicle design, cost and other aspects to competition judges. Teams then compete for a higher portion of points through dynamic events, which include skidpad, acceleration, autocross, and endurance events.
When I joined Formula Kentucky, the team was very young. FSAE teams had previously existed at the University of Kentucky (the first team at UK started around 1996), but many of these groups had failed and disbanded. In 2014, the existing team members decided to re-brand UK FSAE as Formula Kentucky, and since then, the team has been performing consistently. In 2016 (at the end of my freshman year), the team was able successfully complete its first full competition at FSAE Michigan with its first competitive car, FK01. During my sophomore and junior years, I was able to help get the team through two more consecutive years of competition. The team has now been able to complete the endurance event for three consecutive years with three different vehicles - FK01 (competed in 2016 FSAE Michigan), FK02 (competed in 2017 FSAE Michigan), and FK03 (competed in 2018 FSAE Lincoln). This was an incredible accomplishment for the team because during a typical FSAE competition, only one-third to one-half of the competing teams are able to finish the endurance event.
Near the end of my sophomore year, I transitioned into becoming the team’s Aerodynamics/Bodywork Lead. Traditionally, aerodynamics was not a critical concern for the team because reliability and low cost are the main areas of focus for young teams. When building FK02 during my sophomore year, the team was very short on manufacturing time and financials, so the aerodynamics and bodywork was largely not a priority. However, the team wanted to heavily improve its performance in design judging the following year, which allowed for a case for proper aerodynamics and bodywork to be made.
The development of the next vehicle, FK03, provided me with a clean slate for a fresh start on Computational Fluid Dynamics (CFD) simulations and brand-new composite bodywork. I performed various CFD simulations using ANSYS Fluid Flow CFX and developed a standardized procedure for the team to follow when investigating a given vehicle’s aerodynamic performances. When I was designing the bodywork for FK03, these CFD simulations were used to compare the aerodynamic forces of FK02 (the previous vehicle) to FK03’s conceptual designs. As the team opted to have a non-winged vehicle for FK03, the main goals of aerodynamic design were to reduce drag and lift as much as possible; analyzing the CFD simulations proved that the bodywork for FK03 was able to reduce the forces that FK02 saw.
However, design was only half of the project - manufacturing the bodywork for FK03 provided its own unique challenges. In order to make custom carbon fiber body panels, I had to understand the fundamentals of composite manufacturing. Based on the initial design, positive molds were created by CNC routing polyurethane foam. Wet fiberglass layups were then performed on these positive molds in order to create negative molds, which were ultimately used for the final carbon-fiber/honeycomb parts. Throughout this entire process, the team and I gained a significant amount of experience with mold-making, wet layup processes, and post-layup surface treatment.
When it came time to perform during competition, FK03’s new bodywork proved itself during design judging. At FSAE Lincoln 2018, we were told by the judges that FK03 had arguably the best “non-wing package” bodywork present at the competition. This led to the team’s highest score in the aero/body category in its history of competing. As the team will use FK03 once again for 2019 FSAE Michigan, my current focus has been on improving the fundamental CFD models that I initially created, validating and correlating results with real-life testing, and exploring the use of wing elements for future vehicles.
In addition to serving as Aerodynamic/Bodywork Lead, I have devoted a lot of time on work similar to my work with the UK Solar Car Team, including improving the team’s fundraising and marketing abilities, handling various administrative tasks and challenges, maintaining an image and vision for the team, and so on. The technical and non-technical experiences I have had with Formula Kentucky have truly shaped me to become a better engineer and understand what it takes to be competitive in an engineering setting.
For more information about Formula SAE and Formula Kentucky, please visit www.sae.org/attend/student-events and facebook.com/FormulaKentucky.
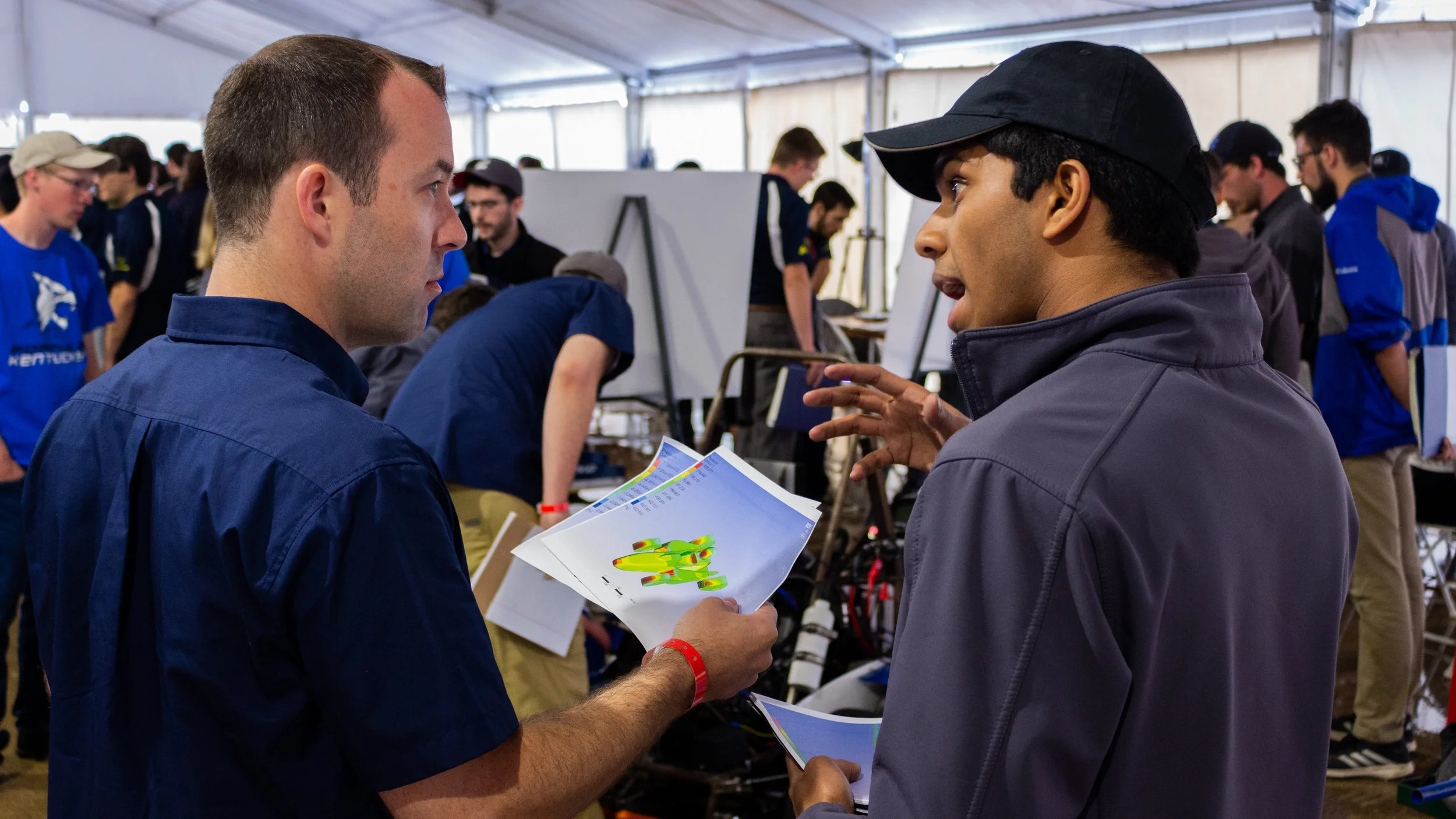



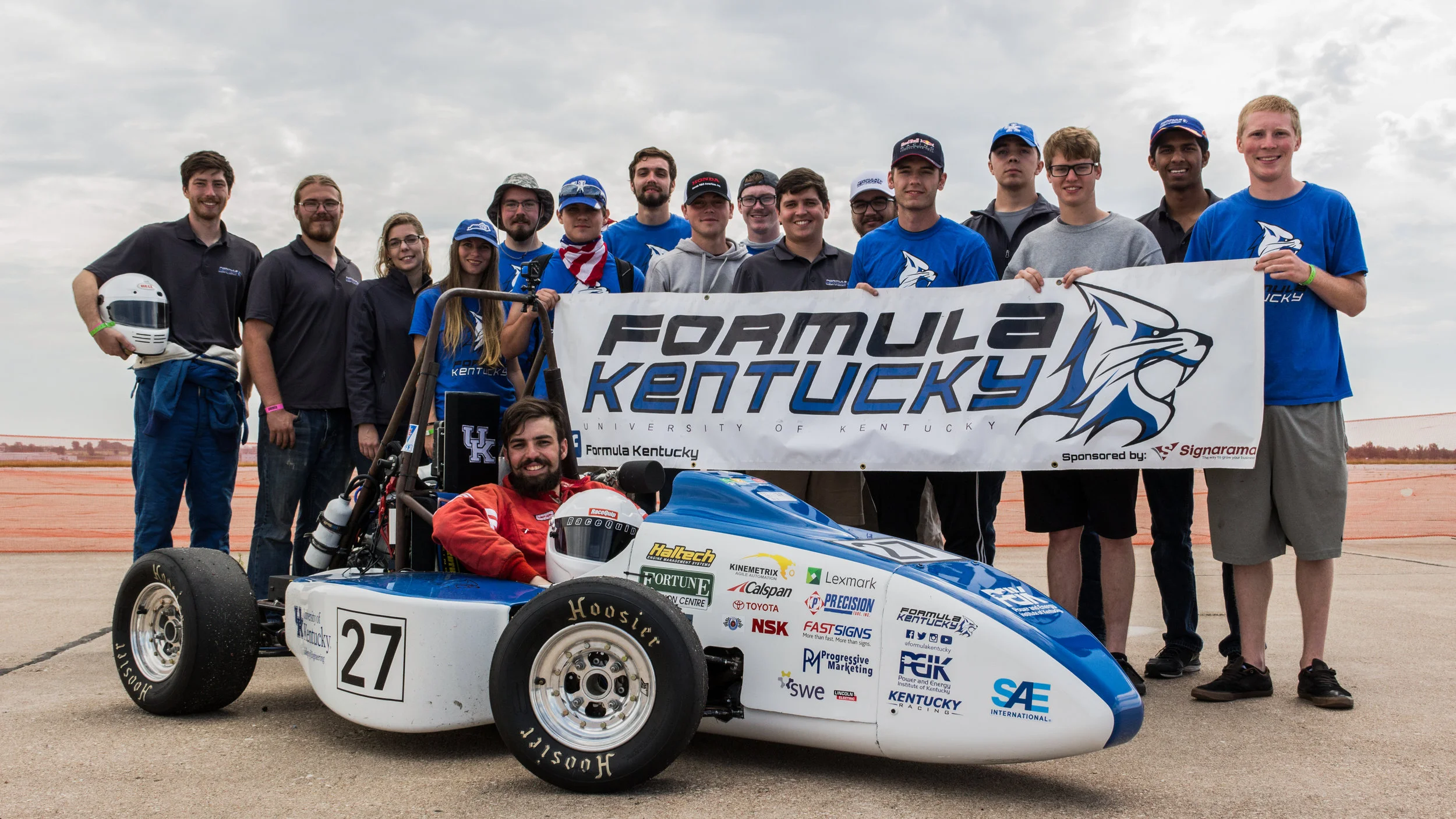